We are thrilled to share the exciting news of our successful collaboration with Damen Naval at their Vlissingen-Oost shipyard. The recent implementation of PipeCloud has already started to make a significant impact on their pipe production and monitoring activities, and we are proud to see the impressive early results.
Here’s the full story as published in Damen Naval’s internal newsletter:
Schelde Schakels, June 2024: PipeCloud at Vlissingen-Oost
PipeCloud is live and the results can already be seen
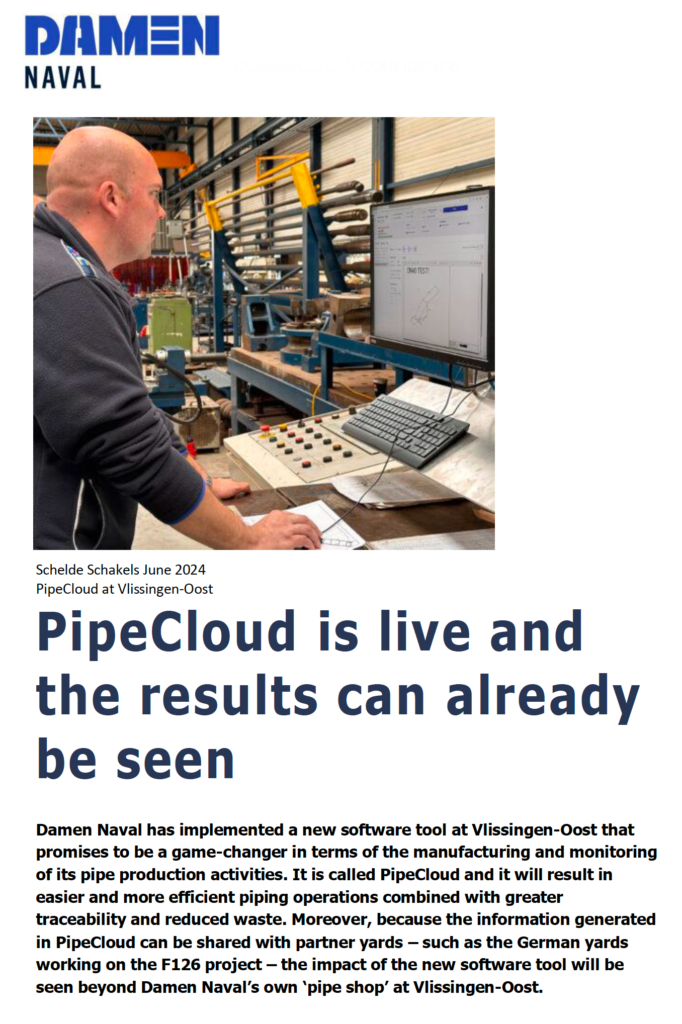
Damen Naval has implemented a new software tool at Vlissingen-Oost that promises to be a game-changer in terms of the manufacturing and monitoring of its pipe production activities. It is called PipeCloud and it will result in easier and more efficient piping operations combined with greater traceability and reduced waste. Moreover, because the information generated in PipeCloud can be shared with partner yards – such as the German yards working on the F126 project – the impact of the new software tool will be seen beyond Damen Naval’s own ‘pipe shop’ at Vlissingen-Oost.
Damen Naval’s piping team will use PipeCloud primarily in its manufacturing engineering processes; these serve as the link between engineering and manufacturing. For many years, these have been carried out manually, as Damen Naval’s Manufacturing Engineer Piping Marco Gabriëlse (pictured above) says. “We would use various Excel sheets to create things like material lists or spool lists. Or an old programme for the pipe-bending machines. Now with PipeCloud, we can do everything automatically.”
PipeCloud will result in simpler and more efficient piping operations
“We receive two types of files from our engineering department,” Marco explains. “A PDF, which shows what the finished pipe should look like, and a PCF which is the pipe component file, which contains all the technical details of the pipe coordinates, materials, joints, bends and endings. All we have to do is click and drag the PDF and PCF into PipeCloud. And then PipeCloud generates the delivery package – containing all the information that a pipe-fitter needs: a list of materials, cutting lists, bending information, label print list and spool lists.” In addition to being paperless, the use of PipeCloud will also optimise the so-called ‘pipe nesting’ (best described as: how many sections of pipe can be cut out of one long piece of pipe), thus reducing material waste and human error.
Despite only being implemented so recently, PipeCloud is already proving its worth. First of all, it is fast. “It takes about 10 minutes to prepare delivery packages for approximately 50 pipes,” says Marco. Furthermore, it enables coordination with partner yards, which comes in handy during the various international projects Damen Naval is working on.
The piping team will mainly use PipeCloud in production engineering processes
Either at its own pipe shop at Vlissingen-Oost or one of its partner yards, the implementation of PipeCloud will give Damen Naval’s manufacturing engineering team more control of the entire pipe production process. This includes planning, monitoring and traceability. “This is now so straightforward. PipeCloud’s to-do list and calendar gives us this oversight, showing exactly what has been done and what still needs to be done. I am very happy with this new piece of software tooling. It will save us a lot of time, really increasing our efficiency,” concludes Marco.
Celebrating Our Successful Collaboration
At PipeCloud, we value strong partnerships and seamless cooperation. Working with Damen Naval has been an exemplary experience, demonstrating the power of collaboration and innovation. Their openness to integrate new technology and our commitment to delivering cutting-edge solutions have made this project a resounding success.
Stay tuned for more updates as PipeCloud continues to innovate and drive efficiency in the piping industry. For more information about our solutions and how we can help your business achieve similar results, contact us today!