Joonas Väätänen, a young foreman at Ardor Ltd. was interviewed by Sales Director, Atte Peltola, about how PipeCloud paperless production has changed everyday work for him at Ardor.
What are the benefits the PipeCloud system has brought to the shop floor?
“You can easily see that all the preconditions are ready for fitting. PipeCloud shows you the status of all the previous work phases, so you don’t have to run around the factory with papers trying to figure out if the fitting work can start or not.
Another typical challenge we face is with unforeseen absences. If one of the guys working on a large fitting work order falls ill and must go home, it used to take quite a lot of effort to figure out the status of the work order. In PipeCloud, you can see the work order status directly and precisely, which makes it much easier to transfer it to another person to continue the work.
Monitoring progress is really easy now. You can simply see it in PipeCloud in real time, rather than hunting down the status from each worker separately. There is also much less chance for human error when work orders are in the system and visible via the screens. Misplaced paper drawings and work orders are a thing of the past.
Another really great improvement is the ability to report blocked work orders directly via touchscreen. If there are some missing materials, for example, you can input the information about what’s missing and it goes directly to the warehouse via the PipeCloud system.
In general, having all the relevant information easily available when work progresses from one person to the next is a crucial feature.”
What is your typical day like at Ardor?
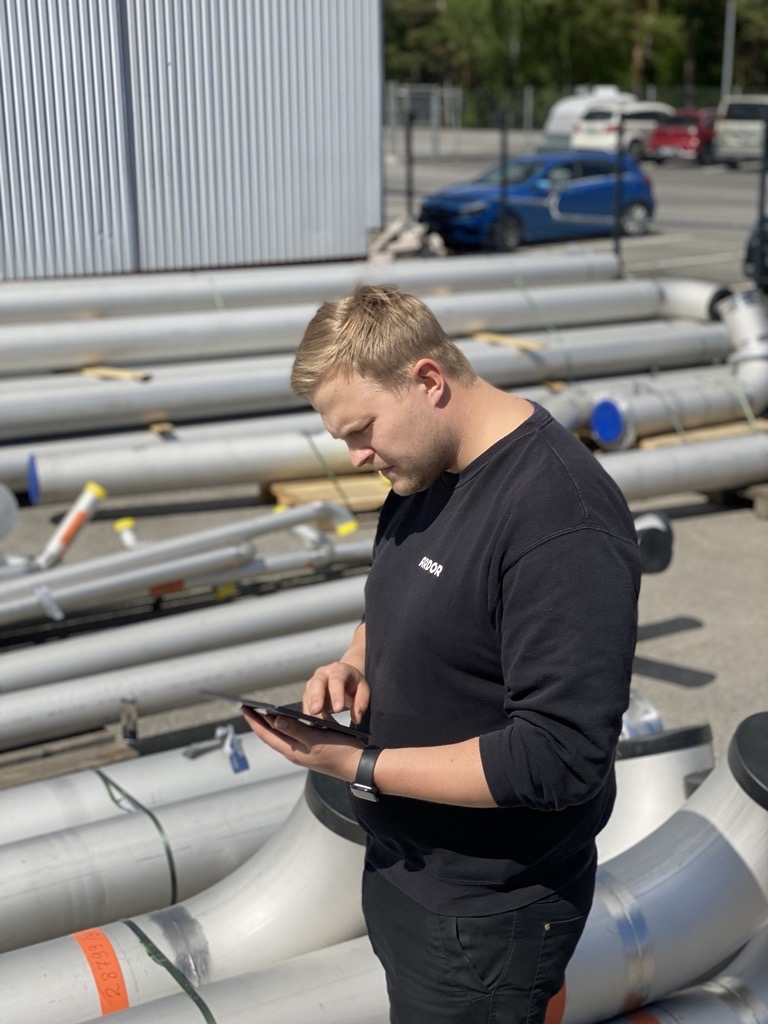
“I always start by saying good morning to the guys on the shop floor. After that, I usually start by checking the production tickets from the previous afternoon. It is normally the responsibility of the work planner to follow them, but I want to ensure that nothing is forgotten. These production tickets are created by the workers via the touchscreens at their workstations. If they have a problem that is blocking their work, I can check what is causing the problem. I also assign new work orders to different resources via PipeCloud.
Before we went paperless, I had to print and distribute the work orders to the workers by hand. Now I can just assign them in the system and the workers see them in their own individual “My bundles” view. Even though I’m responsible for ensuring that the work orders are done in the right order, it’s so easy to manage that sometimes it is not even necessary for me to assign them. PipeCloud automatically sorts and schedules the work orders according to the delivery time. This means that I don’t have to run around the factory to ensure that the right work is done at the right time, nor do I have to do detailed scheduling because PipeCloud does it semi-automatically.
It feels like I am just supporting PipeCloud when needed. This collaboration between me and the technology frees up a lot of time for me to find potential areas for improvement in the production line.”
So, PipeCloud has made things more efficient?
“Absolutely! Problem solving is so much easier now with PipeCloud. In the past, if I found a piece of pipe lying on the shop floor, I would have to ask the workers who was responsible for it. If no-one knew due to someone being on holiday or something, I would have to find the drawing and start to investigate where the pipe belongs. Nowadays, I can figure out exactly where the pipe needs to be in a matter of seconds using my smartphone.
Quality assurance has also been dramatically improved. Previously, the heat numbers were written by hand on the assembly drawing, which made it quite difficult to read out and summarize on the QA delivery documentation. At worst, this was 1 – 2 days’ work. Now, I get an automatically generated report straight from PipeCloud.”
Are there any other benefits you have noticed with PipeCloud?
“In general, all the necessary production information is available on my smartphone via PipeCloud. This means that all the issues that come up during the day can be clarified within seconds. In PipeCloud, every action is tracked. This is extremely beneficial if there is a customer claim for welding. I don’t have to guess who welded that particular pipe; I can see it directly in PipeCloud. If there is a geometrical mistake done in fitting, thanks to PipeCloud, there is no need to publicly investigate who made the mistake. Instead, I can simply address the issue privately with the person responsible, go through the mistake and the corrective actions on how to avoid it in the future. If certain mistakes are repeated, I can also follow up on them and use them as examples when planning future training and instructions for the workers. Ultimately, all this improves quality and efficiency.
Ardor is a Finnish company producing digitally prefabricated pipes for shipbuilding and industry. Ardor began operations in 1988 under the name Konepaja Sipilä & Hyvärinen, which later became Sihy. Nowadays Ardor employs almost 100 people. https://ardor.fi/en/